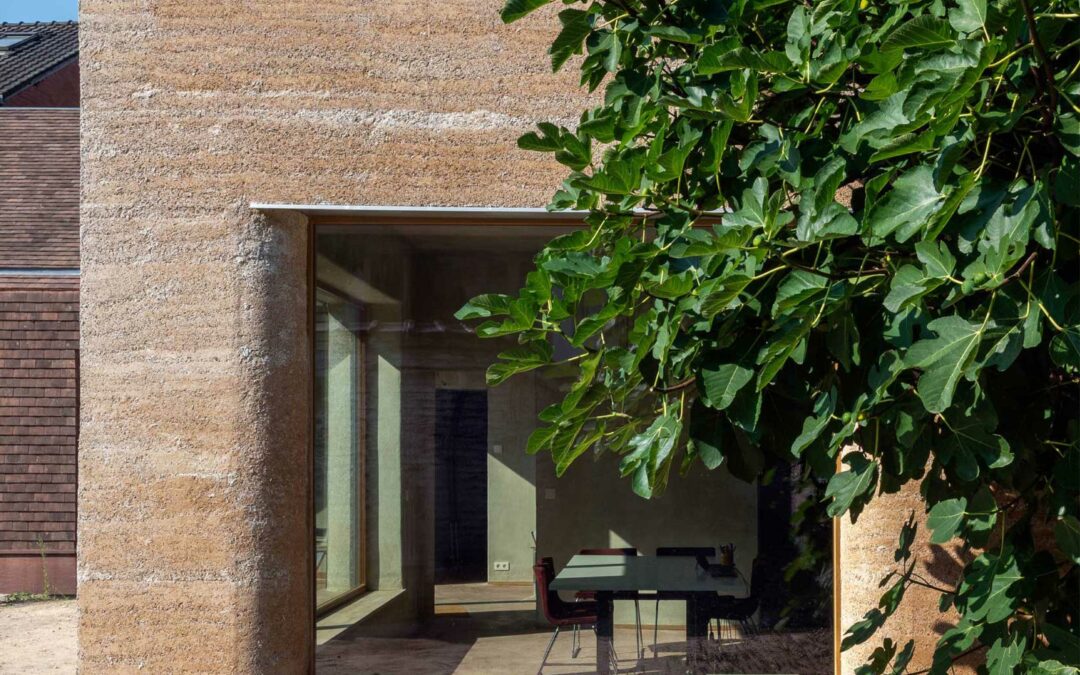
GROW
GROW
GROW: Transformation and Revitalization of a Parking Lot
Description: Multifuncional space, architecture atelier and a thematic urban garden
Type of project: Social , Landscape
Type of customer: Private
Department: Transformation
Location: Forest, Brussels (BE)
Surface area: 400 m²
Year: 2020-2024
Landscape Design: Jérémy Hermant
Photographe: Delphine Mathy
videos archiUrbain: ARCHI URBAIN (19/02) : Decoster (1/2) + ARCHI URBAIN (19/03) : Decoster (2/2)
The GROW project is located at 25 Rue Pierre Decoster, in an inner block accessible from the street via a carriage entrance and a 30-meter paved lane. The site once housed disused stables, sheds, and garage boxes.
The aim of the project is to preserve and transform the existing buildings while reducing empty spaces, notably by demolishing certain garages. This frees up space for a green interior that promotes biodiversity, permeability, and shared spaces.
The program calls for the creation of new workspaces, including our architectural offices and paramedical practices, all connected by a large multi-purpose room that opens onto a shared outdoor space.
The multi-purpose room, along with the creation of a themed vegetable garden, is designed to host projects and initiatives at a neighborhood scale. Numerous associations, schools, and neighborhood groups are located in the immediate vicinity, paving the way for a variety of collaborations, allowing the project to take root in the community.
An Ecological, Sustainable, and Circular Approach
The GROW project, winner of the RENOLAB program for both the design and execution phases, was closely monitored. Site visits organized by Brussels Environment coordinators and managers enabled a series of exchanges, advice, and verification of compliance with the ecological and technical commitments made during the design phase.
From an architectural standpoint, the project focused on maintaining the existing structure while adopting a coherent, sustainable approach in the choice of materials and technical solutions, without compromising the desired aesthetic quality.
We prioritized the conservation of structural elements, the integration of openings into existing bays, and the reuse of materials on-site.
In addition to reuse, one of the guiding design principles was economy of means: each material must fulfill multiple functions. The choice of materials was driven by sustainability criteria while respecting economic feasibility and the project’s contextual requirements.
Hemp concrete was used to insulate part of the facades. Hemp concrete not only functions as insulation but also serves as an exterior finish. A key criterion in choosing this material was its recyclability after dismantling. Studies on this are currently underway, and initial results suggest that 100% of the material could potentially be recovered to produce new hemp concrete.
As companies specializing in biosourced and natural materials are still rare in Belgium, this project was partly experimental, particularly in the production of the hemp concrete façade. This was carried out by volunteers in a participatory worksite supervised by Laurane Coornaert of Degré 47.
The participatory worksite created a pleasant atmosphere, fostering exchanges, learning, and encounters. The hemp concrete was installed similarly to rammed earth techniques: a modular formwork was attached to the wooden framework of the façade for the formwork phase.
Reclaimed roof tiles and façade cladding were used to create a coherent aesthetic. The composition of these walls and roofs can be entirely dismantled (two layers of insulation, rainscreen, battens, tiles), with a large proportion being potentially reusable. For example, the roofing contractor estimated that only 5% of the tiles were lost during the first dismantling operation, and if the building were dismantled at the end of its life, 50% of the tiles could be recovered.
The garage floors were paved. After dismantling them, we created a breathable floor structure consisting of a shell aggregate (considered a waste product in the sand industry), which contributes to insulation and acts as an effective barrier against capillary rise. The insulation was provided by 25 cm of hemp lime. For the interior finish, we designed a screed based on the Roman concrete method, using lime and terracotta aggregates.
Recycled clay plaster and cork blocks were chosen for the interior finish not only for their aesthetic appeal but also for their hygroscopic and acoustic properties.